ورق گالوانیزه یکی از محبوبترین انواع محصولات فولادی است که در بین ورقهای فولادی موجود در صنعت روز دنیا، کاربرد و اهمیت ویژهای دارد. برای تولید ورق گالوانیزه دو روش اصلی وجود دارد که گالوانیزه گرم به دلیل سرعت بالای تولید خود به مراتب بیشتر مورد استقبال قرار میگیرد. اما همانطور که شما نیز ممکن است بارها با این مشکل روبرو شده باشید، جوشکاری قطعاتی که با گالوانیزه پوششدهی شدهاند همواره با مشکلات اساسی روبرو بوده است. این موضوع زمانی حیاتیتر میشود که مقاطع نازک مانند ورق گالوانیزه را بخواهیم جوشکاری کنیم. در این مقاله میخواهیم به چالشهای موجود بر سر راه جوشکاری ورق گالوانیزه میپردازیم و احتمال انجام جوشکاری ورق گالوانیزه را بررسی میکنیم.
فهرست این مطلب
عوارض و مشکلات جوشکاری گالوانیزه
همانطور که گفته شد، همواره جوشکاری مقاطع گالوانیزه برای اپراتورها مشکل بسیار بزرگی بوده است. به دلیل وجود این مشکل، تولیدکنندگان عموما محصول خود را به طور کامل و نهایی آماده میکنند و پس از آن کل قطعه را گالوانیزه میکنند، اما در برخی از کاربریها چنین امکاناتی برای تولیدکنندگان فراهم نبوده و نیاز به جوشکاری را ناگزیر میکند. اما این مشکلات شامل چه مواردی میشود؟
۱-ایمنی و سلامت جوشکار
یکی از دلایل بازدارنده برای عدم جوش ورق گالوانیزه، حفظ سلامت جوشکار است. قطعهای که دارای پوشش گالوانیزه باشد در اثر تماس با الکترود جوشکاری در منطقه متاثر از حرارت، پوشش خود را از دست میدهد. زینک اکساید (ZnO) که پوشش گالوانیزه است در تماس با فرایند جوشکاری ذوب و حتی بخار میشود. این ماده نسبتا سمی است و استنشاق طولانی مدت آن میتواند حتی باعث مرگ شود. از این رو، همواره سختگیریهایی برای استفاده از جوشکاری روی قطعات گالوانیزه وجود دارد. برای رفع این مشکل، جوشکار موظف است علاوه بر پوشش و تجهیزات معمول جوشکاری که شامل دستکش، محافظ چشم و لباس مخصوص است، از ماسک مخصوصی نیز استفاده کند که اثر بخار زینک اکساید را به حداقل برساند. تصویر این ماسک در زیر نشان داده شده است.
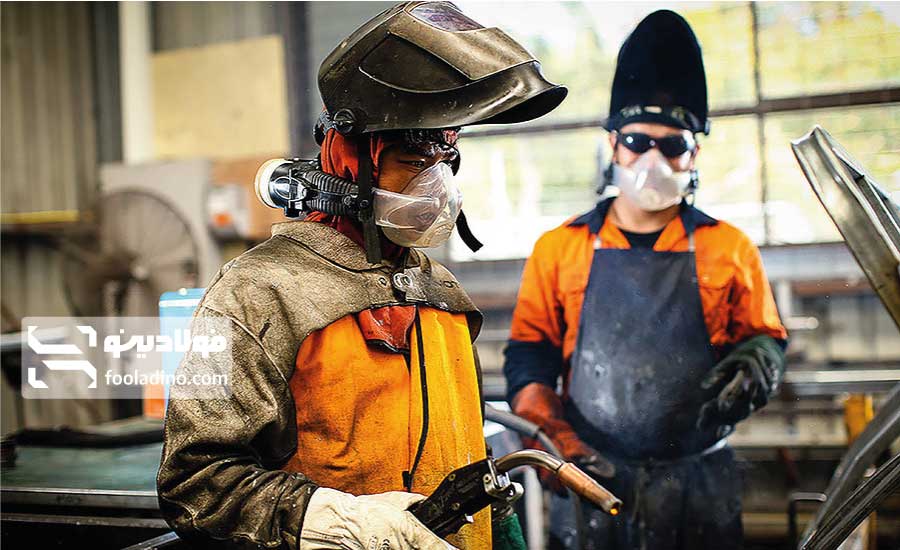
جالب است بدانید حتی با وجود استفاده از ماسک، هنگامی که اجبار به جوشکاری گالوانیزه باشد، کل فرایند باید در مکانی انجام شود که دارای تهویه هوای بسیار مناسب است.
۲-تضعیف مقاومت به خوردگی
پیشتر گفته شد که حرارت ناشی از جوشکاری، پوشش گالوانیزه را در ناحیه جوش از بین میبرد. همچنین؛ ناحیه جوشکاری شده به دلیل حرارتی که به صورت ناگهانی تحمل میکند، عموما خواص مکانیکی ضعیفتری نسبت به سایر نواحی قطعه کار دارد. ترکیب این دو مشکل با هم باعث میشود که ناحیه جوشکاری شده قطعه گالوانیزه نه استحکام کافی داشته باشد و نه مقاومت به خوردگی مناسب که هدف اصلی استفاده از گالوانیزه است. یعنی در واقع جوشکاری پس از گالوانیزه باعث میشود که قطعه تولید شده تفاوت چندانی با حالت بدون پوششدهی خود نداشته باشد.
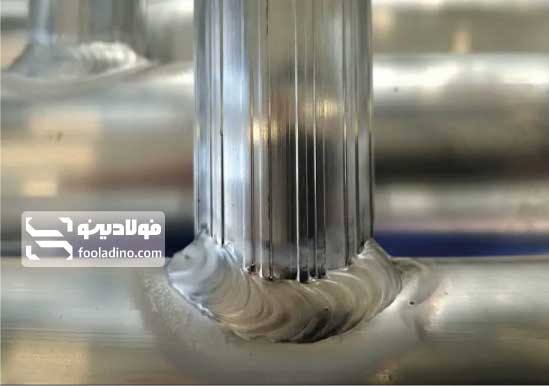
توجه به این نکته بسیار حائز اهمیت است که هرچه ضخامت قطعه گالوانیزه کمتر شود، آسیب ناشی از جوشکاری نیز افزایش پیدا میکند چرا که حرارت ناشی از مذاب جوش به آسانی در کل قطعه پخش میشود. به همین دلیل است که جوش ورق گالوانیزه نسبت به سایر محصولات فولادی چالش برانگیز تر است.
عوامل موثر بر جوشکاری گالوانیزه
علیرغم مشکلات مطرح شده، در برخی شرایط، نیاز به جوشکاری ورق گالوانیزه اجتناب ناپذیر است. راهکارهایی برای به حداقل رساندن آسیبهای ناشی از جوشکاری وجود دارد که به برخی از آنها اشاره میکنیم.
۱-حذف پوشش گالوانیزه پیش از جوشکاری
برای کاهش ریسک جانی، بهتر است که پوشش گالوانیزه در ناحیه جوش به صورت مکانیکی تا حد امکان از بین برود. برای این کار میتوان از سنباده زنی قطعات کمک گرفت. در صورتی که امکان حذف پوشش فراهم نبود، توصیه شده است که از الکترودهایی استفاده شود که مخصوص قطعاتی است که با زینک پوشش داده شدهاند. پس از انجام جوشکاری، نواحی جوش داده شده مجددا باید به صورت نقطهای پوششدهی شوند.
۲-انتخاب صحیح نوع پوششدهی گالوانیزه
مطالعات نشان دادهاند که هرچه پوشش ورق گالوانیزه نازکتر باشد، کیفیت جوشکاری بهتر میشود. از این رو؛ توصیه میشود ورق گالوانیزهای که تحت جوشکاری قرار میگیرد، به وسیله روش گالوانیزه سرد (الکتروپلیتینگ) تولید شده باشد چرا که گالوانیزه گرم ضخامت بیشتری از پوشش گالوانیزه را ایجاد میکند. همچنین؛ ورق گالوانیزه سرد پوشش یکدستتری دارد که کیفیت جوش را ارتقا میبخشد.
منبع
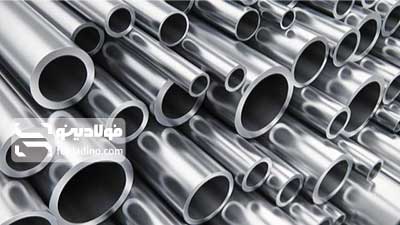
انواع روشهای جوشکاری ورق گالوانیزه
تا کنون متوجه شدیم که جوشکاری ورق گالوانیزه با مشکلات زیادی روبرو است. با این وجود، راهکارهای نسبتا مناسبی برای انجام جوشکاری پیدا شده است. در ادامه به معرفی دو روش کاربردی در جوشکاری ورق گالوانیزه میپردازیم.
۱-جوشکاری ورق گالوانیزه با CO2
جوشکاری قوس الکتریکی در پناه گاز محافظ (MIG) یکی از روشهای جدید جوشکاری به حساب میآید که به واسطه خواص و شرایطی که فراهم میکند، مورد استقبال گسترده تولیدکنندگان قرار گرفته است. در این نوع جوشکاری، جریان مداوم از یک گاز خنثی نظیر آرگون و یا CO2 به ناحیه جوش دمیده میشود. این کار باعث میشود که آلودگی و اکسید در ناحیه جوش تشکیل نشود و از میزان آسیب به ناحیه جوش کاسته شود.
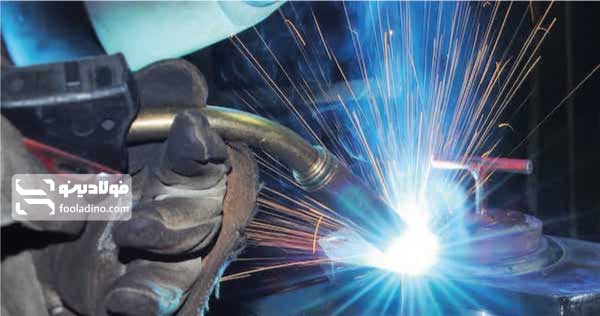
۲-جوشکاری ورق گالوانیزه با اینورتر
کاربرد اینورتر به این صورت است که توانایی تغییر برق متناوب شهری (AC) به برق مستقیم (DC) و سپس تغییر مجدد آن به برق متناوب با ولتاژ و جریان دلخواه را دارد. این قابلیت به اپراتور جوشکار این امکان را میدهد تا با ولتاژ متناوبی کمتر از ولتاژ شهری جوشکاری خود را انجام دهد. این کاهش ولتاژ باعث میشود که منطقه متاثر از جوشکاری بر روی قطعه به حداقل برسد و کمترین آسیب متوجه پوشش گالوانیزه شود. اینورتر برای مقاطع نازک راهکاری موفق است. از این رو، جوشکاری ورق گالوانیزه با اینورتر در حال گسترش روز افزون است.
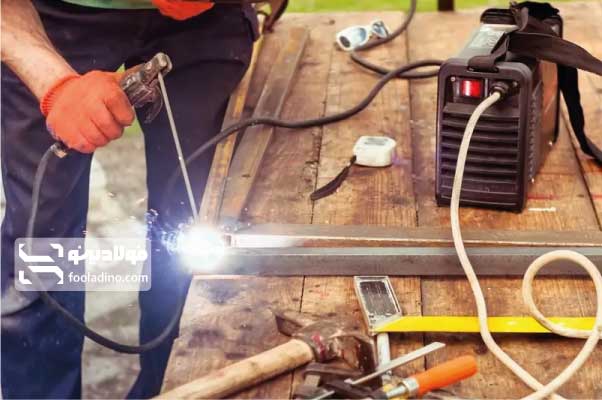
الکترود و سیم جوش ورق گالوانیزه
همانطور که تاکنون آموختیم، تنها گونههای محدودی از انواع روشهای جوشکاری برای کار روی ورق گالوانیزه کاربرد دارد. اگر برای جوشکاری ورق گالوانیزه از روش MIG به همراه گاز CO2 استفاده شود، سیم جوش مناسب به صورت کلاف و در دستگاه جوشکاری قرار میگیرد و به صورت مداوم ناحیه جوش را تغذیه میکند. اما در صورتی که الکترود مورد استفاده قرار گیرد، توجه به این نکته ضروری است که الکترودی مناسب جوشکاری است که مخصوص فلزات پوشش داده شده با زینک باشد.
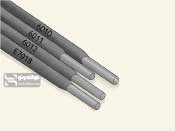
جمعبندی
در این مقاله تلاش شد چالشهای پیش رو برای جوش ورق گالوانیزه و مشکلات احتمالی به دقت بررسی شود. پس از آن با مدنظر قرار دادن مشکلات موجود، راه حلهایی کاربردی برای جوشکاری روی گالوانیزه ذکر شد. در ادامه نیز الکترودهایی که میتوانند برای این جوشکاری مورد استفاده قرار بگیرند، ارزیابی شد. برای مشاهده سایر مقالات وبسایت فولادینو اینجا کلیک کنید. فولادینو ارائه دهنده کلیه مقاطع آهن آلات و فولادهای آلیاژی موجود در بازار است و شما عزیزان میتوانید از طریق لینک زیر به روزترین قیمت تمامی محصولات را در این وبسایت مشاهده کنید.
.