شکلدهی فلزات را میتوان یکی از مهمترین شاخههای مهندسی و علم مواد به شمار آورد. توسعه روشهای گوناگون برای ایجاد مقاطع و محصولات در ابعاد و ضخامتهای گوناگون، این امکان را در اختیار سایر صنایع مانند ساختمان سازی، خودروسازی و انواع سازههای مهندسی قرار داده است که خلاقیت و ابتکار عمل بیشتری در طراحیهای خود داشته باشند و موفق به تولید سازههایی شوند که به لحاظ زیبایی ظاهری و خواص ارائه دهنده، در سطوح بالاتری قرار گرفتهاند. در این مقاله تلاش میشود تا شما را با متعارفترین روشهای شکلدهی فلزات آشنا کنیم.
فهرست این مطلب
ریختهگری یا شکلدهی فلزات؟ کدام یک مناسب ساخت قطعه نهایی است؟
ریختهگری یکی از قدیمیترین و گستردهترین روشهای ساخت محصولات فولادی است. حال این سوال پیش میآید که اگر امکان تولید قطعات به روش ریختهگری فراهم است، چه نیازی به تولید قطعات به روش شکلدهی است؟
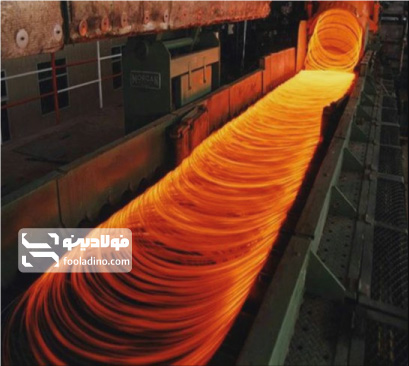
برای پاسخ به این سوال، چند دلیل عمده وجود دارد؛ دلیل اول به خواص ضعیفتر قطعه ریختهگری شده در مقایسه با همان قطعه تولید شده با شکل دهی فلزات دلالت دارد. ظاهر قطعات ریختهگری ده سطح مناسبی ندارند و به دلیل تحت فشار نبودن، کار سخت نشده و استحکام بالایی از خود نشان نمیدهند. همچنین قطعات ریختهگری شده، میتوانند دارای حفرات و تخلخلهای سطحی و عمقی باشند و کارایی قطعه را از بین ببرند. ریختهگری قطعات بسیار کوچک و قطعات پیچیده نیز به لحاظ زمانی و اقتصادی، توجیه ندارد. با توجه به مباحث گفته شده و اینکه امکان بالا رفتن هزینه تولید قالبهای ریختهگری وجود دارد، از ریختهگری بیشتر برای شمشریزی استفاده میشود و تولید قطعات نهایی به انواع روشهای شکلدهی فلزات واگذار میشود.
انواع روشهای شکلدهی فلزات
با پیشرفت تکنولوژی، روشهای گوناگونی برای شکلدهی فلزات اختراع شد. هر کدام از روشهای موجود در کاربریهای خاصی بهترین عملکرد را دارند. به همین دلیل، همگی این روشها در مکان مناسب خود مورد استفاده قرار میگیرند و نمیتوان گفت روشی بر روش دیگر برتری دارد. در ادامه برخی از مهمترین روشهای شکل دهی فلزات را مرور میکنیم:
۱- فورج یا آهنگری
آهنگری از دیرباز به عنوان فرایندی کلیدی برای شکلدهی فلزات، مورد استفاده قرار میگرفته است. مهمترین کاربرد آهنگری در قدیم، در ساخت تسلیحات و ادوات جنگی بوده است. انواع شمشیر، زره و نعل اسب به کمک آهنگری ساخته میشده است. در ادامه در دنیای مدرن امروزی، آهنگری با نام فورج به فعالیت خود ادامه میدهد. فورج در بزرگترین کارخانهها به صورت تمام اتومات انجام میشود. نحوه انجام فرایند فورجینگ به این صورت است که نمونه بر روی سطح کار قرار میگیرد و از بالا و یا به صورت همزمان از دو یا چند جهت، فشار سنبه به قطعه وارد میشود و در چند مرحله، شکل نهایی به وجود میآید.
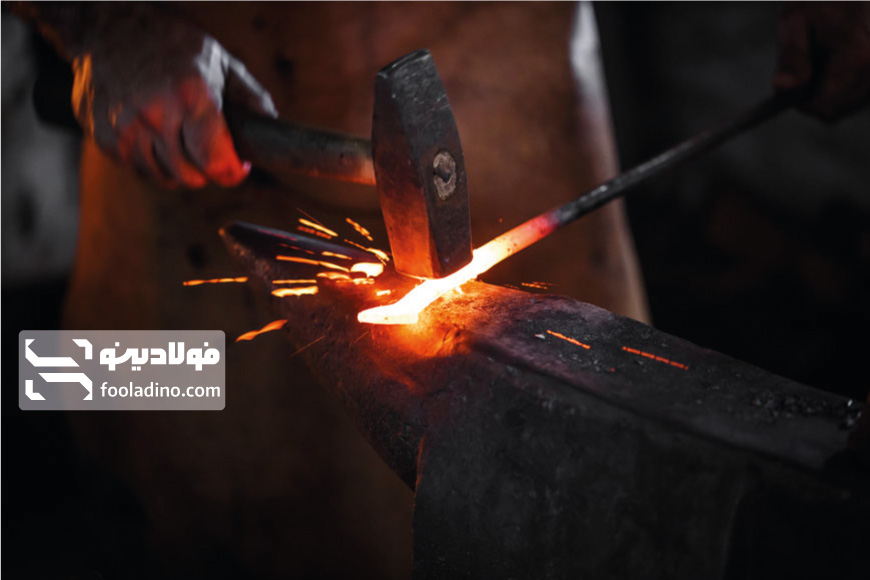
لازم به ذکر است قطعات تولید شده به روش فورج از کیفیت سطحی و استحکام بسیار بالایی برخوردار خواهند بود.
۲- فرایند نورد برای شکلدهی فلزات
فرایند نورد را میتوان انقلابی در صنعت تولید مقاطع فولادی به حساب آورد. کلیدیترین مقاطع نظیر ورق، تیرآهن و میلگرد از طریق فرایند نورد تولید میشوند. اساس کار نورد به این صورت است که قطعه مورد نظر بر روی خط تولید قرار میگیرد و با عبور از بین دو غلطک در بالا و پایین، رفته رفته ضخامت خود را از دست داده و به شکل نهایی تبدیل میشود.
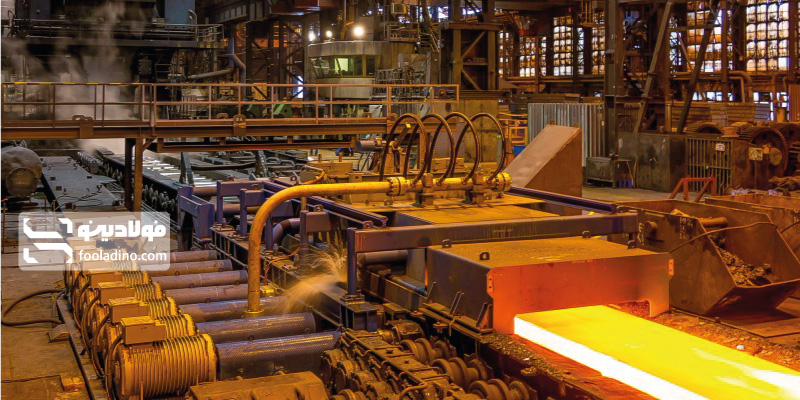
این فرایند به دو صورت نورد گرم و نورد سرد انجام میشود که در ادامه به تفکیک به هرکدام میپردازیم:
۲-۱-نورد گرم
نورد گرم برای تولید مقاطع پرکاربرد با خواص متوسط، بهترین گزینه به حساب میآید. نکته مهم در این فرایند این است که قطعات مورد استفاده برای نورد گرم، پیش از انجام فرایند، پیشگرم میشوند. پیشگرم سازی به اصطلاح فولاد را کمی نرم میکند و شکلدهی را آسانتر میکند. در نورد گرم، مقاطع در چندین پاس رفت و برگشتی از زیر غلطکها عبور میکنند و برای جلوگیری از آسیب رسیدن به خط تولید، آبپاشی به صورت مداوم انجام میپذیرد. کارخانه فولاد مبارکه اصفهان یکی از مهمترین کارخانههای تولید کننده ورق سیاه به روش نورد گرم به شمار میرود.
۲-۲-نورد سرد
نورد سرد عموما برای تولید ورقهای با پوشش خاص به کار میرود. یکی از تفاوتهای عمده نورد سرد با نورد گرم این است که در این فرایند، امکان تولید محصولات با ضخامت بسیار کمتر نیز فراهم میآید. ورق روغنی و ورق گالوانیزه، مهمترین محصولات تولید شده به کمک فرایند نورد سرد هستند.
۳-ورق کاری برای شکلدهی فلزات
یکی از فرایندهای شکل دهی بسیار پرکاربرد ورق کاری است. در این روش، ورقهای تولید شده در نورد گرم یا سرد به وسیله تجهیزات به صورت اتوماتیک، نیمه اتوماتیک و یا دستی به محصول نهایی تبدیل میشوند.
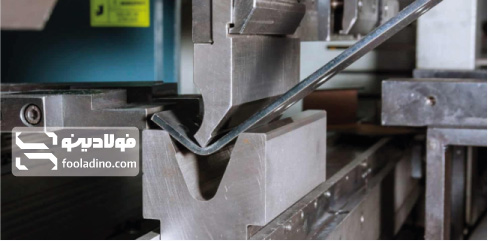
مهمترین محصولات تولید شده به کمک این فرایند عبارتند از:
- انواع قوطی پروفیل،
- مقاطع پروفیل رو باز و بسته
- لولههای درز مستقیم
۴-متالورژی پودر برای شکلدهی فلزات
استفاده از پودر فلزات، در دوران قدیم و در نقاط مختلف دنیا معمول بوده است. مصریها پودر آهن را ۳۰۰۰ سال پیش از میلاد مسیح به کار گرفتهاند، ستون شهر دهلی هندوستان نیز به این روش در ۳۰۰ سال بعد از میلاد مسیح بنا نهاده شده است، این ستون تقریبا از ۶/۵ تن پودر آهن اسفنجی ساخته شده است. با وجود این که از نظر تاریخی، متالورژی پودر از قدیمی ترین روشهای شکل دهی فلزات است، اما تولید در مقیاس تجاری با این روش، از جدیدترین راه های تولید قطعات فلزی به شمار میرود. در دوران باستان از روشهای متالورژی پودر برای شکل دادن فلزات با نقطه ذوب بالاتر از آنچه در آن زمان داشتند، استفاده میشد.
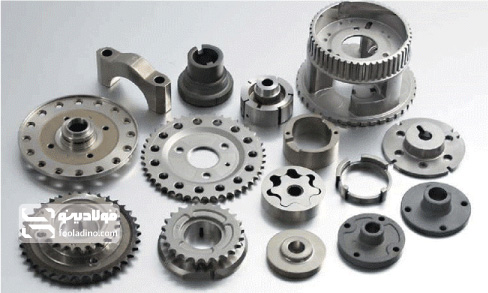
متالورژی پودر روشی برای ساخت و تولید قطعات فلزی و سرامیکی است که اساس آن بر فشردن پودر مواد به شکل مورد نظر و تف جوشی آن است. تف جوشی در درجه حرارتی زیر نقطه ذوب صورت میپذیرد.
۵-شکلدهی فلزات به روش اکستروژن
اکستروژن یکی از راهکارهای نسبتا جدیدی است که از آن برای تبدیل بیلت به قطعه نهایی در یک مرحله، استفاده میشود. برای تولید محصول به کمک اکستروژن، بیلت در محفظه کار قرا میگیرد. در سمت دیگر قالبی طراحی شده است که دارای سطح مقطع توخالی از مقطع نهایی است. بیلت با فشار رم به سمت سوراخ هدایت میشود و شکلدهی نهایی انجام میشود.

۶-کشش سیم
متداولترین روش تولید انواع مفتول و توری، کشش سیم است. در این فرایند، میلگرد ساده به صورت شاخهای از یک دهانه با قطر مشخص کشیده میشود و میلگرد طی چند مرتبه کشش، به مفتول تبدیل میشود. توجه به این نکته ضروری است که نباید میلگرد را به صورت شدید دچار تغییر قطر کرد چرا که احتمال پارگی در اثر کشش به شدت افزایش مییابد.
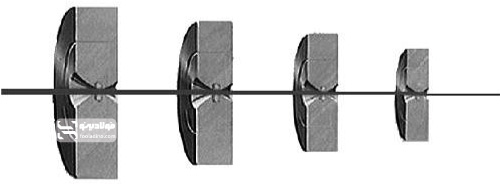
فرایند شکل دهی مقاطع مختلف
به طور کلی، دو عامل بسیار تاثیرگذار در تولید انواع مقاطع آهن آلات تاثیر دارد. فاکتور اول سرعت تولید انبوه این محصولات است و دومین مساله، هزینههای مورد نیاز برای تولید هر کیلوگرم از آن محصول. با در نظر گرفتن این دو عامل میتوان اینگونه گفت که فرایند نورد گرم در بیشتر موارد بهترین گزینه برای تولید انبوه و شکل دادن فلزات به حساب میآید. به طور کلی برای تولید انواع ورق، میلگرد و تیرآهن از نورد گرم کمک گرفته میشود. سایر مقاطع همانند لولههای درزدار، نبشی و ناودانی منتج از ورق هستند پس میتوان گفت این مقاطع نیز به صورت غیر مستقیم از نورد حاصل میشود و سپس به کمک تجهیزات مناسب ورق کاری، به فرم نهایی خود در میآیند.
دستگاه شکلدهی فلزات
برای تولید مقاطع مختلف از ابزار آلات و دستگاههای متفاوتی استفاده میشود. به عنوان مثال؛ در فرایند نورد گرم، مهمترین ابزاری که فرایند شکلدهی فلزات را برای خطوط تولید میسر میکند، استفاده از غلطکهای نورد است. این غلطکها در ابعاد و جنسهای مختلف تولید میشوند و هدف نهایی آنها نیز رسیدن به شکل نهایی مورد نظر است. برای شکل دادن ورق و تبدیل آن به نبشی، ناودانی و یا لوله نیز از یک خط تولید بسیار ساده استفاده میکنند. اساس کار دستگاه ورق کاری به این صورت است که ورق پس از تابگیری وارد پروسه تولید میشود. پس از آن به کمک غلطکهای موجود در دستگاه شکل دهی فلزات به شکل مقطع نورد نظر نهایی مثلا لوله در میآید. در مرحله نهایی نیز به کمک جوشکاری مقاومتی به لبه محصول تولید شده به هم متصل میشوند و محصول نهایی آماده بهرهبرداری است.
جمعبندی
در ای مقاله به معرفی انواع روشهای شکلدهی که حجم تولید بالایی دارند پرداخته شد. این فرایندها شامل فورج، نورد، اکستروژن، متالورژی پودر و کشش سیم است. شما عزیزان میتوانید برای مطالعه مطالب مشابه روی این لینک کلیک کنید. همچنین برای نگارش این مقاله از این مطلب کمک گرفته شده است. شما عزیزان میتوانید برای مشاهده وبسایت فولادینو و آگاهی از جدیدترین قیمت انواع مقاطع آهنی و ساختمانی از مسیر زیر اقدام نمایید: